Engine Simulation Test System (EST)
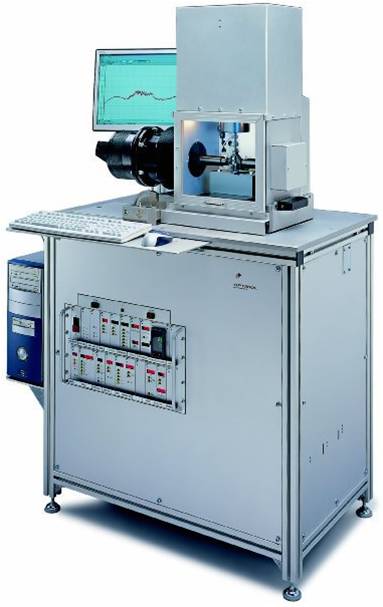
The SRV® technology platform from Optimol Instruments has a modular structure. This allows the configuration to be seamlessly adapted to individual testing requirements. To further optimize compatibility with specific test and analysis projects, a wide range of specimens, specimen holders and adapters are available. Based on the proven SRV® technology platform, simulations, measurement and testing projects as well as tribological analyses can be carried out in an enormous variety.
The engine simulation test system is based on the SRV4, supplemented by the RAI – or nVCT test system, which allows highly accurate recording of wear rates in the range of nanometers per hour using radioactively marked test specimens….
Test principle of the basic device Oscillation |
The two test specimens installed in the test chamber (e.g. ball on disc) are pressed onto each other with a specified normal force. The upper specimen oscillates on the lower specimen. Frequency, sliding distance, test force, test temperature and test duration are specified. The friction forces are continuously measured by a sensor. The friction coefficient is automatically calculated and recorded during the entire test duration. Wear is measured and recorded during and/or after the test. |
Testing principle of the Rotation option |
The rotation module is an alternative motion system to oscillation. Its main components are the rotary motor, the motor for the displacement of the block (radius) and the multi-channel sensor for measuring torque and friction. After removal of the oscillation pick-up block, a device with rotating disk is installed. The counterbody (e.g. pin/ball/disk) is installed in the existing test load system by means of an adapter. The triborelevant variables of frictional torque and frictional force are measured via a multi-channel sensor system. The rotation block is equipped with a heater and a temperature sensor. |
Wear measurement with nVCT® radionuclide technology |
nVCT® opens up the possibility of measuring nano-wear using radionuclide technology with high precision and efficiency already in the SRV® model test environment. Radionuclide technology (RNT) is a long-established method for continuous measurement of wear. Due to its complexity, it could previously only be used effectively on engine test benches. |
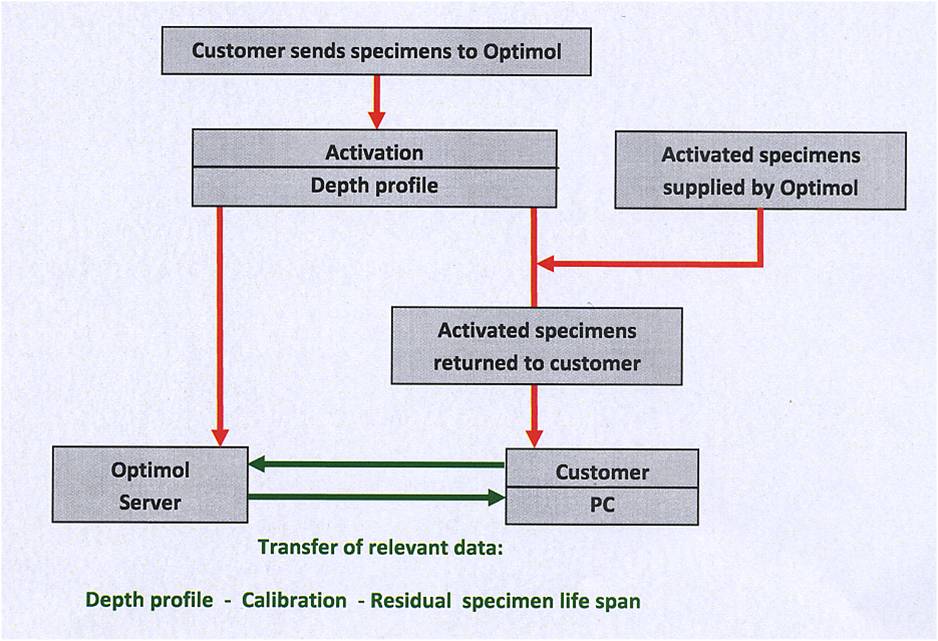
With the development of the nVCT® technology by AC2T research GmbH, the analysis possibilities of the RNT method could be opened up for the first time for application in the model testing environment of the SRV® test system. These analysis capabilities primarily include continuous measurement of nano-scale wear, the 2-isotope technique, determination of realistic wear rates as a basis for extrapolating system life, differentiation between run-in and constant wear, and the possibility of mechanism-based wear investigations. |
Test bench parameters | ||
Frequency/speed | 1 to 500 Hz / 0 – 2000 1/min. | |
Stroke/radius | 0.1 to 5 mm (at max. 50 Hz) / 0 – 42 mm | |
Load | 1 to 2,500 Newton | |
Temperature | -40 to 900 °C | |
Ambient medium | Nitrogen, synt. Air, conditioned air 10 – 90 % rel. F. | |
Movement type / form | Glide (oscillation) | |
Friction conditions | Solid, boundary and mixed friction | |
Contact geometry | Point, line and surface contact | |
Measured variables | Friction value, linear wear amount, opt. Assessment, contact resistance |
DIN tests
- Determination of friction and wear parameters for lubricating oils; DIN 51834-2; ASTM D6425-05
- Determination of the tribological behavior of materials in interaction with lubricants; E DIN 51834-3
- Testing the tribological serviceability of transmission/hydraulic fluids, E DIN 51834-4
- Tribological testing of bonded dry lubricants on the translational oscillation tester; E DIN 51834-8
- Determination of friction and wear parameters for grease-lubricated plastic sliding couples; E DIN 51834-9
- Textile machinery and accessories – Needle and sinker lubricating oils for knitting machines – Part 1: Minimum requirements for mineral oil based oils; DIN 62136-1
- Diesel fuel method for the determination of lubricity using a vibration wear tester; DIN ISO 12156-1
Tests according to international standards
- ASTM D 5706-05 and E DIN 51834-5: Standard Test Method for Measuring Friction and Wear Properties of Lubricating Greases Using A High-Frequency, Linear-Oscillation (SRV) Test Machine (EP Properties of Greases)
- MASTM D 5707-05 and E DIN 51834-6: Standard Test Method for Determining Extreme Pressure Properties of Lubricating Greases Using A High-Frequency, Linear-Oscillation (SRV) Test Machine (Friction and Wear Properties of Greases)
- ASTM D7217-05: Standard Test Method for Determining Extreme Pressure Properties of Solid Bonded Films Using a High-Fequency, Linear-Oscillation (SRV) Test Machine
- ASTM D7421-08: Standard Test Method for Determining Extreme Pressure Properties of Lubricating Oils Using a High-Fequency, Linear-Oscillation (SRV) Test Machine
- ASTM Working Group 15940: Standard Test Method for Determining Tribomechanical Properties of Grease Lubricated Plastic Socket Suspension Joints Using a High-Fequency, Linear-Oscillation (SRV) Test Machine
- Vibration friction wear test for lubricants (SRV) according to TRW in-house standard for cardan shaft greases (plastic joints) (TRW 62051301)
- EN 1071: Reciprocating Wear Test for Ceramic Coatings [CEN/TC 184/WG5 Document N148)
- ASTM-Working Group: Standard Test Method for Tribological Characterisation of Piston Ring and Cylinder Liner Materials and Lubricants using SRV Test Machine
- ASTM Working Group: Measuring Fretting Wear and Resistance of Lubricating Grease under High Hertzian Contact Pressures Using a SRV Test Machine
Possible specimen geometries
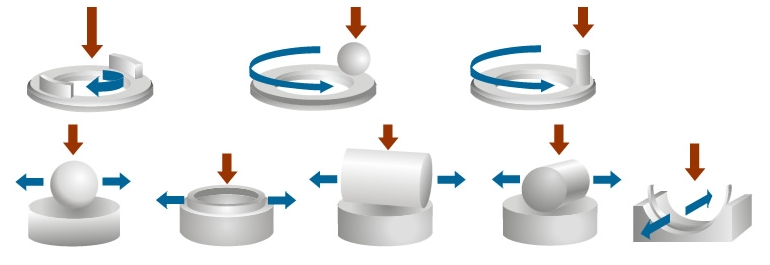