The “two-disc test stands
“Amsler A135” and “Optimol Instruments 2disk”.
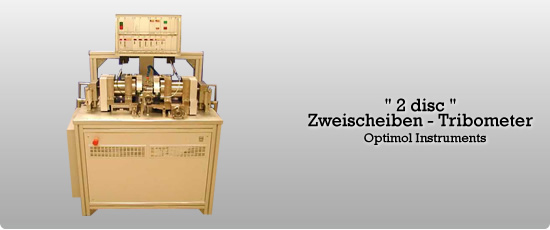
Two-disk test rigs are used to investigate the motion types rolling, sliding and tumbling.
They can be used, for example, to model the motion processes on tooth flanks.
Two-disc test stand “A135 |
The two-disk test rig “A135” from Roell-Amsler can be used to investigate the motion types rolling, sliding and tumbling. |
As standard, two 10 mm wide discs with a diameter of 40 mm are pressed together. Theoretically, the lateral surfaces of the disk can have any conceivable geometry. The frictional torque is recorded continuously. Wear can be determined after the test by weighing or measuring. With the switchable eccentric, a pulsating radial load (abrupt lift-off) can be superimposed on the rotary motion. A second eccentric allows periodic axial back and forth movement of the upper specimen. When the upper shaft is stationary, a bearing half-shell can also be used instead of the cylindrical specimen in order to test plain bearing materials and coatings, for example. |
Two-disc test stand “2disc |
The modern two-disc test rig “2disc” from Optimol-Instruments, Munich, can be used to investigate the motion types rolling, sliding and tumbling. As standard, two 10 mm wide cylindrical discs with a diameter of 45 mm are pressed together here. Theoretically, however, the shell surfaces of the disks can have any conceivable geometry. For higher pressures, crowned washers are used, for example. |
The frictional torque is recorded continuously. Wear is detected during the run via an inductive sensor. After the test, the mass wear can be determined by weighing. |
In contrast to the old two-disk test stands from the Roell-Amsler company, this state-of-the-art tribometer has significantly greater performance data and much higher precision. |
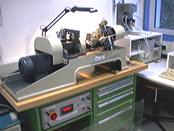
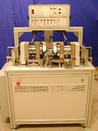
Test bench parameters | A 135 | 2disc | |
Normal force | 20 to 2000 N | 20 to 5,000 N, by means of spring and servomotor | |
Rotary speed | 25 to 350 1/min | 0 to 3000 1/min, one servo motor (27 Nm) per shaft | |
Temperature | RT | RT (oil circulation up to 80°C) | |
Movement types | Glide, roll, roll | Rolling (synchronous operation), sliding (standstill of a shaft, counter-rotation), rolling (stepless slip) | |
Slip | 0%, 10% | 0 to 100% | |
Friction conditions | Solid state, boundary and mixed friction, elastohydrodynamics | Solid state, boundary and mixed friction, elastohydrodynamics | |
Contact geometry | Point, line contact | Point, line contact | |
Measured variables | Continuous friction torque measurement | Continuous friction torque measurement, IR temperature on specimen, continuous wear measurement on specimen, slip, speed, normal force | |
Specimen | Width 10 mm, Ø 40 – 65 mm | Width 10 mm, Ø 45 mm (max. Ø 60 mm) | |
Sliding speed | 0.1 to approx. 2.7 m/s | 0.1 to max. 18.8 m/s (in counter-rotation) |
Other tests
- Characterization of the friction and wear behavior of materials and coatings
- Determination of traction curves of oils (e.g. for CVT transmissions)
- Investigation of rolling strength and fatigue strength of materials in lubricated and non-lubricated condition
- Characterization of the friction and wear behavior of materials
- Investigation of material and lubricant properties under rolling and antifriction stresses
- Simulation of wheel/rail wear stress (driving surface) and curve area (tramway)
Possible specimen geometries
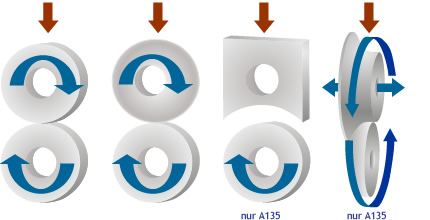